The Issue of Rare Earth Dependence
The F-35 joint strike fighter is arguably the crown jewel of US military hardware. Yet in 2022, the exquisite aircraft caused embarrassment when it was revealed that its engine required a rare earth magnet produced only in China.
Rare Earths (REs) are a group of 17 elements, including neodymium, terbium, and dysprosium, and scandium. They are not particularly rare – all are more common than gold – but they are fiendishly difficult to separate into usable forms. When embedded in technologies, REEs become invisible to consumers.
That makes them no less essential to national and economic security. The Congressional Research Service notes that every F-35 contains over 400 kgs of rare earth materials, while Virginia Class Submarines contain over 4 metric tons of rare earths.1
Rare Earths and Selected Applications2
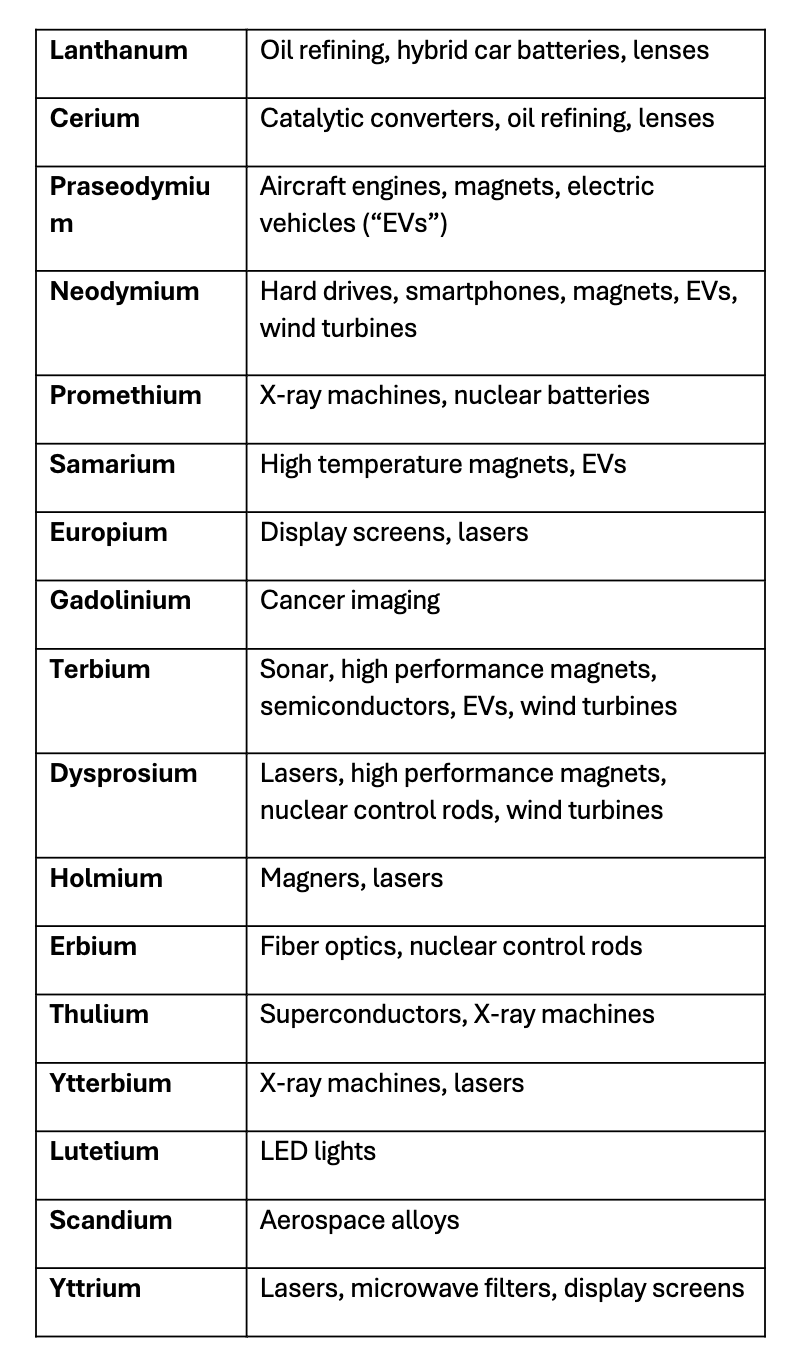
Following the 2022 revelation of the Chinese RE magnets, F-35 production was halted. Yet only one month after the embarrassing revelation, DoD signed a waiver to enable F-35 deliveries to continue – Chinese magnets included – while the agency searched for a domestic replacement for the RE magnets.
The F-35 magnet debacle begs the question: how did America’s military find its prestige hardware reliant on components sourced from China? The answer is simple. China mines and refines most of the world’s Rare Earths, and dominates the downstream supply chain. Reducing vulnerability to RE supply weaponization will require rebuilding integrated RE separation and refining supply chains outside of China.
Rare Earth Markets & Supply Chains
With no centralized marketplace, data on prices and production of REs is sketchy. Estimates of the size of the global RE market are typically well under $10 billion per year.3
While concentrated RE ore might cost only dollars per kilo, refining and separating the RE can cost tens or even hundreds of dollars per kilo. RE processing plants also cost hundreds of millions or even a billion dollars to establish.4 With a relatively small annual market size, the economics of opening new refining operations to compete with China’s are delicate.
While China controlled up to 95% of global RE mine production in 2010, competitors have claimed increasingly large shares of RE mining over the past decade. Notably, as of 2024 Australia (5%) and the US (12%) have accelerated mine production.5 Importantly, no country monopolizes reserves. Nevertheless, the most profound chokepoint in today’s RE supply chain is processing, where China still controls approximately 90% of global capacity.6
The US was a RE super-power between the 1960s and 1990s, but today, China processes most of the RE ore mined in the USA.7 Decades of Chinese state support and tightening environmental regulations since the 1970s incentivized the concentration of the global RE industry into China. Despite a ten-fold price spike in REs in 2010 caused by shrinking Chinese export quotas and fears of RE “weaponization”, the US Geological Survey estimates that the US remains approximately 95% important for its REE needs, 75% coming from China – a number which would doubtless be higher if it included all REE-containing intermediate and finished products.
In today’s high-tech world, Rare Earths find their way into everything. Erbium improves the fiber optic cables providing Wi-Fi to your home, while Cerium powder smooths iPhone screens. Despite the panoply of applications for REs, their most important use is in high strength magnets.
Magnets are not, on the face of things, strategically important. Nonetheless, if you’ve ever felt an iPhone vibrate or heard the whirr of a hard drive spinning while you boot up your laptop, then you’ve experienced the magic of a Neodymium, Dysprosium, and Terbium RE magnet. What makes these magnets so important is strength and resilience in harsh conditions. While magnets typically lose their strength when heated, the key benefit of specialized RE magnet alloys is that they can operate at high temperatures required in electronics and defense applications.
The implications of RE magnets for national and economic security are immense. RE magnets power the hard drives needed for data centers and the fin actuators which guide aircraft and precision strike weapons. Put simply, anyone using data centers (Google, Amazon Web, Open AI), or high temperature electronics (every aerospace or defense contractor) needs some REs.8 Concerningly, the Commerce Department has determined that the US is nearly 100% import dependent for the most important types of high quality RE magnets.9
4 key causes underling the RE national security problem
The story of the F-35 RE magnet vividly illustrates the significance of critical minerals, which have become one of the most profound vulnerabilities in western industrial supply chains. The US is critically import dependent for military-grade RE magnets, and the world relies on China RE mining and refining capability. Nevertheless, four key barriers to rebuilding RE supply chains outside of China have kept the US and its allies dependent on Chinese RE.
China’s Mature State-Operated Industry
China’s RE industry produces high quality RE products at better prices than competitors. China’s dominance over RE processing capacity provides power to influence prices. The concentration of industry within China also means that RE supply chains there are efficient and reliable.
This makes it exceedingly difficult for junior western RE companies to compete with more mature and better-connected Chinese competitors. China’s RE industry is also concentrated into state-owned firms capable of weathering years-long cycles of low prices typical of commodities markets.
The nature of China’s mature, concentrated, and state-owned RE industry provides great advantages in selling REs, which have thin margins and high volatility. The largest two publicly traded western RE firms, Lynas Group (Australia) and MP Materials (USA) must, by contrast, satisfy stockholders and survive harsh price cycles.
Pollution Challenges
Proven methods of industrial RE production are highly pollutive and environmentally destructive. Opening new mines and processors requires navigating a regulatory and permitting minefield.
While the small number of RE mines operated by the US and its allies is problematic, refining is the true chokepoint for lessening dependence on China. Concentrating the small fractions of RE found within rocks requires multiple toxic chemicals and concentrates radioactive and heavy metal byproducts that are always found alongside REs.
America’s leading RE mine was shuttered by health authorities over twenty years ago after unreported incidents of radioactive and heavy metal contamination near the mine were discovered by the EPA. Similarly, Lynas Corporation, an Australian RE miner and producer, was forced to shutter most of its RE refining facilities in Malaysia after local authorities discovered elevated radioactivity in the vicinity of the processing facilities.
Coupled Production of Rare Earth's
Any mine containing a concentration of one RE, like lanthanum, will also contain each of the other 17 REs in some ratio. A thorny issue for profit-seeking firms entering the RE industry is that the separation and refining of the most desirable REEs like terbium and dysprosium generates large surpluses of other REEs and associated elements with lower market demand, such as cerium and lanthanum. This situation leads to continued disequilibrium in supply and demand across the 17 REs.
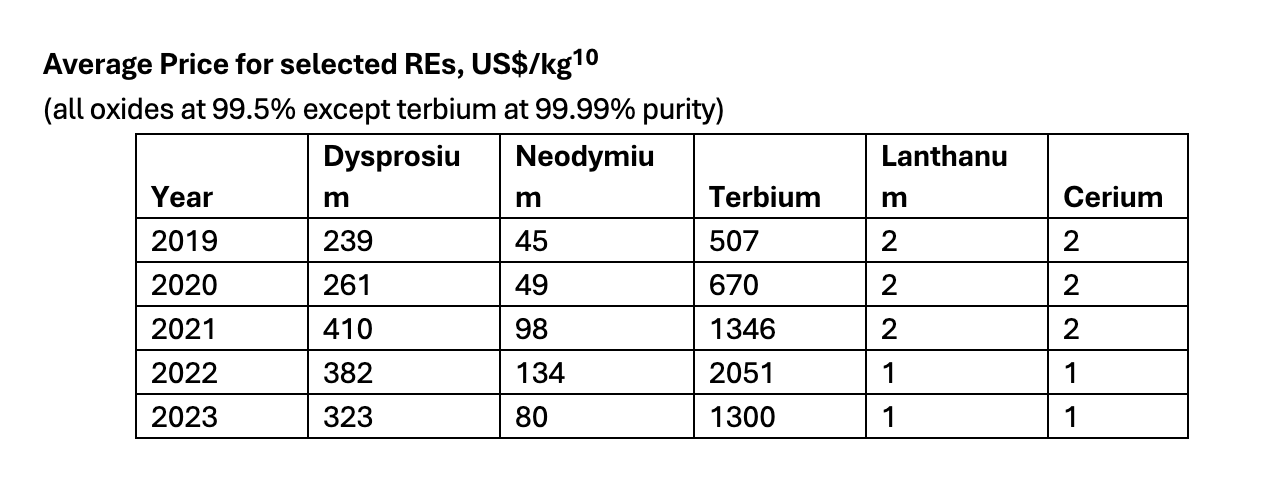
Currently, proven RE processing technologies are built on methods pioneered in the US during the 1940s as part of the Manhattan Project, and separate each RE out from ore one at a time. Finding novel methods of extracting individual REs could not only reduce production of undesired, low-cost REs, but also potentially reduce pollution typical of current RE processing techniques.
Lacking a Rare Earth workforce
The west has experienced decades of brain-drain in its own RE workforce. As RE production concentrated within China during the 1990s and 2000s, so did expertise. This coincided with a general downward trend in mine production in the West. The result: ever fewer American students choose to study mining, geology, and metallurgy, with a nearly 40% drop in graduates from mining engineering programs between 2016 and today.11
Similarly, the number of dedicated mining engineering programs in the US has dropped from 25 in 1983 to 15 in 2023. China meanwhile has over 38 mineral and mining engineering focused schools.
Reducing Dependency on Chinese RE's
The Rare Earth issue is a matter of boosting supply from non-Chinese sources. While this will require opening new sources of raw material supply, the more pressing task is breaking China’s near-monopoly on processing and refining RE into usable forms.
Boosting Supply: The processing bottleneck
Boosting RE raw material supply has attracted both good and bad ideas. While opening more mines will be important, calls to loosen pollution standards, open deep-sea mining, or bypass permitting processes and concerns of local communities surrounding mines can and should be resisted.
Fixing the Rare Earth issue doesn’t require sacrificing environmental protections to open new raw material sources because there are abundant supplies of RE in mine tailings, coal fly ash, and e-waste. The barrier to accessing these supplies is a lack of effective, clean, and economical refining and separation technologies. Disruptive technological solutions should be emphasized, and several already show promise.
REs are often found in concentrated levels in waste of other mineral refining processes, which could be refined to separate the desirable REs into commercially useful forms. One example is coal fly ash, which the US produces over 100 million tons per year of, often containing REs which can be processed.12
Another major untapped RE source is e-waste. The US is a prodigious e-waste producer: millions of tons of air pods, old laptops, and phones are disposed of annually. Yet little of this is captured and recycled to preserve the Res – and other critical minerals – contained within. Much e-waste is simply wasted, even as research demonstrates the feasibility of recycling critical minerals.13 A lack of effective methods for reclaiming critical minerals from e-waste contributes to both a worrying dependence on China and environmental degradation.
It is up to western governments to solve today’s chicken-and-egg problem: if new RE processing technology is possible, but currently expensive and untested at scale, government support can provide a guaranteed demand for clean, de-risked REs while the industry finds its footing.
The Departments of Energy and Defense are already targeting funding at novel processing technologies to process coal ash and recycle e-waste, including with genetically modified bacteria which can be programmed to desirable elements.14 The next step is for the US government to subsidize costs or ensure demand for these products which will, at first, be more expensive than Chinese RE produced with proven but highly pollutive processes.
Reducing Reliance Through Innovation
While there are multiple options to improve RE supply discussed above, for some RE applications, there is also the possibility of reducing demand. Toyota has worked developed new magnet technologies to reduce the need for terbium, one of the most expensive REs, by 80% in their EV motors.
Scientists at Cambridge have also discovered a novel method to produce a RE-free permanent magnet which exhibits similar properties to advanced RE magnets.15 As these examples show, an exclusive focus on increasing production could come at the cost of circumventing the problem via clever disruptive technologies.
Conclusion
Human civilization’s technological progress has often been periodized by the materials we use, from the stone age to the significance of coal and steel for the industrial revolution. Rare earths are among the most important elements powering modern civilian and defense technologies. It is therefore essential to ensure a steady, stable supply of these vital elements.
Solving the issue of rare earth on Chinese processing will require concerted effort from industry, capital, and government. New technologies can help reduce the environmental destruction and pollution associated with the rare earth processing technologies of today, but governments must act to foster innovation, tap into creative supply sources, and support the next-generation of rare earth industry.
References
1 C. Todd Lopez, "DOD Looks to Establish 'Mine-to-Magnet' Supply Chain for Rare Earth Materials," news release, 11 March, 2024.
2 Hyong-Min Kim and Deep Jariwala, The Not-So-Rare Earth Elements, Kleinman Center for Energy Policy (September 23 2021).
3 Tim Worstall, “How to Actually Overcome China’s Rare Earths Monopoly”, The Diplomat, December 9, 2023. Source »
4 Tim Worstall, “How to Actually Overcome China’s Rare Earths Monopoly”.
5 Daniel Cordier, 2024 Rare Earths Mineral Commodity Summary, National Minerals Information Center (2024).
6 Gavin Thompson, “Can the rest of the world repel China’s magnetic pull over rare earth metals?”, Wood Mackenzie, 19 May 2022. Source »
7 Gracelin Baskaran, What China’s Ban on Rare Earths Processing Technology Exports Means. CSIS (8 January 2024). Source »
8 Zane Griffin Talley Cooper, "Of Dog Kennels, Magnets, and Hard Drives: Dealing with Big Data peripheries," Big Data & Society 8, no. 2 (July 1 2021). Russell Parman, “An Elemental Issue”, AL&T Magazine, 26 September 2019. Source »
9 US Department of Commerce, The Effect of Imports of Neodymium-Iron-Boron (NdFeB) Permanent Magnets on the National Security (2022). 7.
10 Cordier, 2024 Rare Earths Mineral Commodity Summary.
11 Thomas Hale, “The United States Needs More than Mining Engineers to Solve Its Critical Mineral Challenges”, CSIS, 8 May 2023. Source »
12 G. Dodbiba & T. Fujita, “Trends in Extraction of Rare Earth Elements from Coal Ashes: A Review”, Recycling, 2023; 8(1):17. Source » C. Scott and A. Kolker, “Rare earth elements in coal and coal fly ash”, US Geological Survey Fact Sheet, 2019.
13 “From trash to treasure: Electronic waste is mined for rare earth elements”, Oak Ridge National Laboratory, August 14, 2019. Source »
14 “DOE Invests More Than $17 Million for Rare Earth Element and Critical Mineral and Material Processing Technologies Using Coal and Coal Byproducts as Feedstocks April 23, 2024”, National Energy Technology Laboratory, 23 April, 2024. Source » “Recovering Rare-Earth Elements from E-Waste”, Defense Advanced Research Projects Agency, 10 June 2022. Source » “Ligand Facilitated Bioaccumulation: Biomining of Rare Earth and Other Critical Metals from Electronic Wastes”, Advanced Research Projects Administration-Energy. Source »
15 Yurii P Ivanov et al. ‘Direct formation of hard-magnetic tetrataenite in bulk alloy castings.’ Advanced Science (2022). DOI: 10.1002/advs.202204315